The term “IoT” or Internet of Things has been a buzzword in the technology industry for the past few years. It refers to the connectivity of physical devices, machines, and objects through the internet, allowing them to collect and exchange data without human intervention. This revolutionary concept has transformed various industries, including manufacturing.
IoT has brought numerous benefits to the manufacturing sector, enhancing efficiency, productivity, and profitability. With the integration of IoT in the manufacturing process, factories can now operate smarter, faster, and more cost-effectively. In this article, we will explore how IoT is revolutionizing the global manufacturing industry.
1. The Rise of Smart Factories
The traditional manufacturing process involved manual labor and machines that were not interconnected. This often resulted in inefficiency, errors, and delays in production. However, with the introduction of IoT, factories have undergone a transformation into what we now call “smart factories.”
Smart factories are equipped with sensors, devices, and machines that are connected through the internet, creating an interconnected network. These factories use real-time data and advanced analytics to optimize operations, increase productivity, and reduce costs. For example, sensors attached to production equipment can monitor performance and send alerts when maintenance is needed, reducing downtime and increasing overall efficiency.
How to Use IoT in Manufacturing
To implement IoT in manufacturing, companies need to invest in the necessary infrastructure, such as sensors, data storage, and analytics tools. They also need to train their workforce to understand and utilize this technology effectively. It is essential to identify areas in the manufacturing process that can benefit from IoT, such as supply chain management, inventory control, and quality control.
Example: Tesla’s Gigafactory
An excellent example of a smart factory is Tesla’s Gigafactory, which manufactures electric vehicle batteries. The factory uses over 300 robots and thousands of sensors to optimize production and improve efficiency. The data collected from these sensors is analyzed in real-time, allowing for better decision-making and reducing the risk of errors.
Comparison: Traditional vs. Smart Factories
The traditional manufacturing process relied on human labor and manual machines, which were prone to errors and inefficiencies. In contrast, smart factories use IoT to automate processes, reduce human error, and increase productivity. Traditional factories also lacked the ability to collect and analyze real-time data, while smart factories can use this data to make informed decisions and improve operations.
Advice: Embrace Digital Transformation
For companies in the manufacturing industry, it is crucial to embrace digital transformation and invest in technology like IoT. By doing so, they can stay competitive, increase efficiency, and meet the demands of the ever-changing market. It is essential to have a clear strategy and plan when implementing IoT to ensure its success.
2. Improved Supply Chain Management
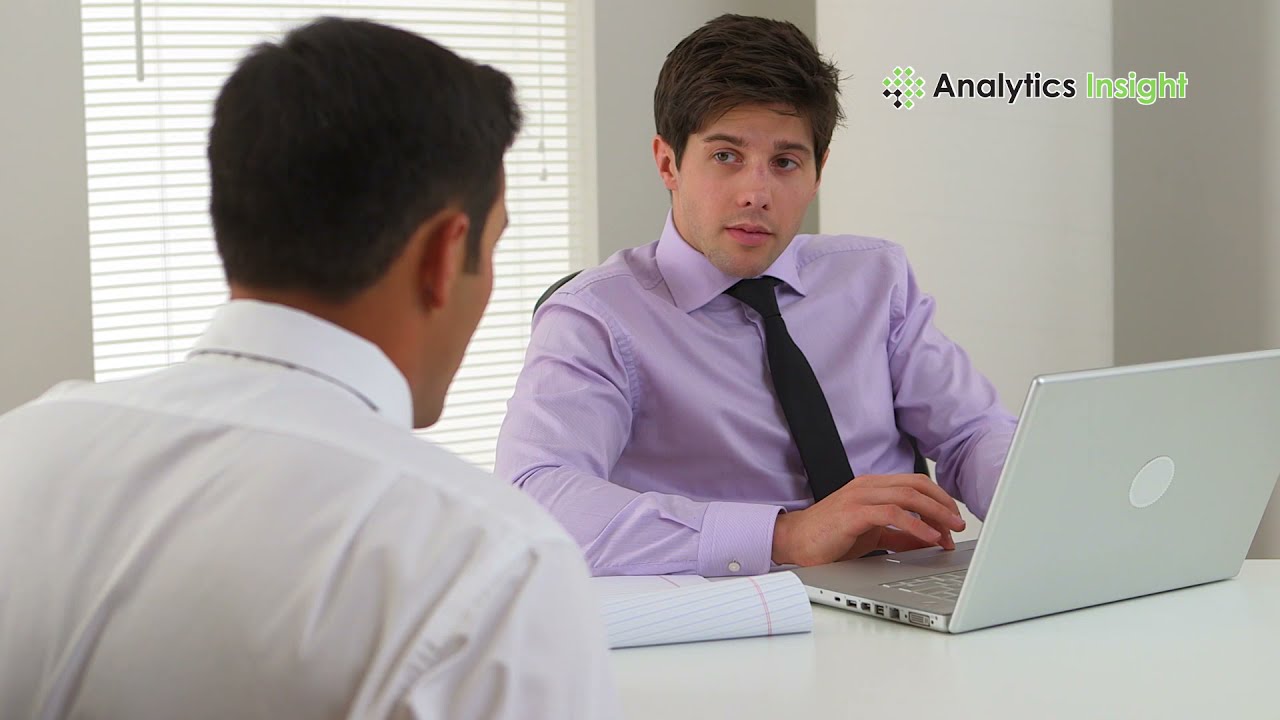
IoT has also transformed supply chain management in the manufacturing industry. With the use of sensors and tracking devices, companies can now monitor their inventory, shipments, and deliveries in real-time. This allows for more accurate forecasting, preventing overstocking or stock shortages. It also enables companies to identify any delays or issues in the supply chain and take corrective action promptly.
How to Use IoT in Supply Chain Management
To utilize IoT in supply chain management, companies need to equip their products, vehicles, and warehouses with sensors and tracking devices. These devices will collect data, such as location, temperature, and humidity, that can be used to monitor the supply chain. Companies can also use this data to optimize routes, reduce transportation costs, and improve delivery times.
Example: Maersk’s Smart Containers
Maersk, one of the world’s largest shipping companies, uses IoT-enabled smart containers to monitor the condition of goods in transit. These containers use sensors to track factors like temperature, humidity, and shock, allowing for better control and security of the goods. This technology has not only improved supply chain management but also reduced losses and damages during transportation.
Comparison: Traditional vs. IoT-Enabled Supply Chain Management
In traditional supply chain management, companies had limited visibility and control over their inventory and shipments. This often led to inefficiencies, delays, and losses. With IoT-enabled supply chain management, companies can track and monitor their products in real-time, improving efficiency, reducing costs, and minimizing risks.
Advice: Collaborate with Suppliers and Partners
To fully harness the benefits of IoT in supply chain management, it is essential for companies to collaborate with their suppliers and partners. By equipping their products with sensors, they can gain insight into the supply chain from end to end. This collaboration allows for better coordination, communication, and optimization of processes, ultimately improving the entire supply chain.
3. Predictive Maintenance
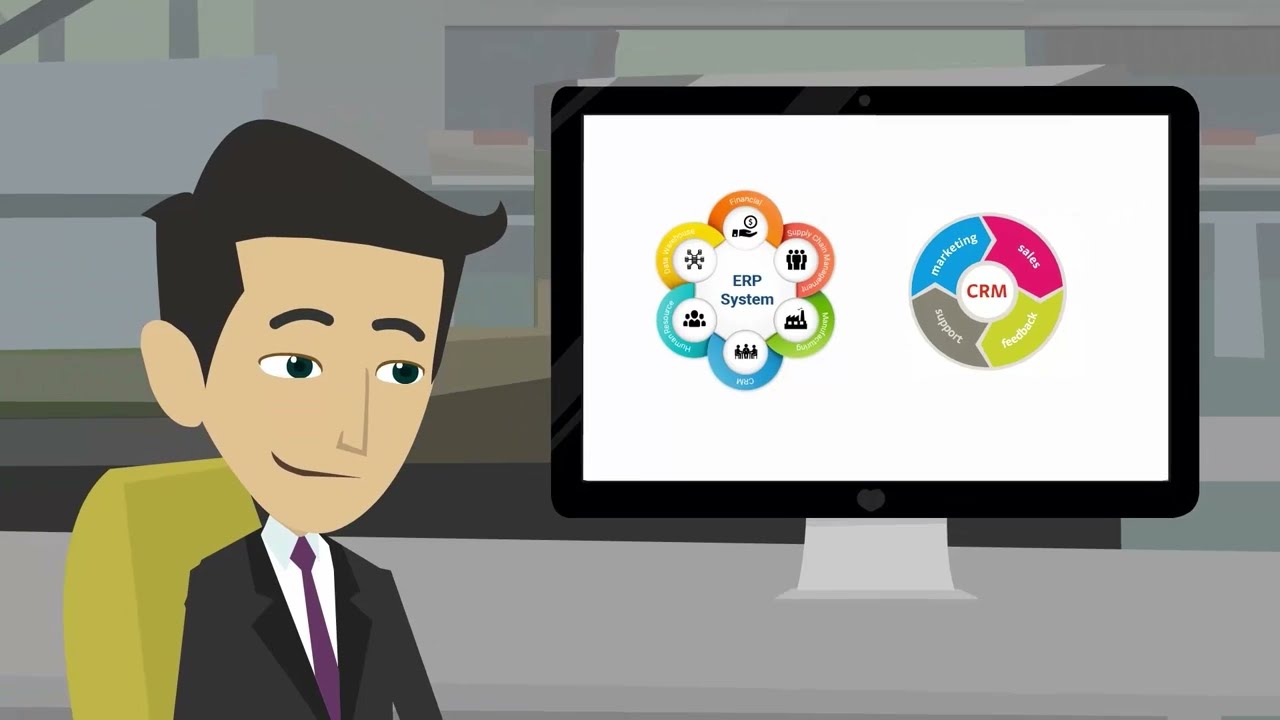
One of the significant impacts of IoT on manufacturing is its ability to enable predictive maintenance. Traditional maintenance methods were based on schedules or reactive maintenance, where equipment was repaired after a breakdown. However, with IoT, manufacturers can use real-time data to predict when maintenance is needed and prevent potential downtime.
How to Use IoT for Predictive Maintenance
To implement IoT for predictive maintenance, manufacturers need to install sensors on machines and equipment that will collect data such as vibrations, temperature, and energy consumption. This data is then analyzed using machine learning algorithms to detect patterns and predict when maintenance is required. Companies can also receive alerts for potential failures and take proactive measures to avoid costly downtime.
Example: General Electric (GE) Aviation
GE Aviation uses IoT-powered sensors to monitor the performance of jet engines in real-time. The data collected is analyzed using advanced analytics, allowing GE to identify any potential issues and take corrective action before a failure occurs. This approach has resulted in a reduction of maintenance costs and increased efficiency in the aviation industry.
Comparison: Reactive vs. Predictive Maintenance
In reactive maintenance, companies wait for equipment to fail before taking action, resulting in costly downtime and repairs. In contrast, predictive maintenance uses real-time data to detect any potential issues and take corrective action before a breakdown occurs. This approach has proven to be more cost-effective and efficient for manufacturers.
Advice: Invest in IoT-Enabled Maintenance Systems
To benefit from predictive maintenance, it is essential to invest in IoT-enabled maintenance systems. Companies need to have the necessary sensors, data storage, and analytics tools to collect and analyze data effectively. It is also crucial to have skilled professionals who can interpret the data and make informed decisions regarding maintenance.
4. Quality Control and Automation
IoT has also significantly impacted quality control in the manufacturing industry. With sensors and cameras attached to machines and products, manufacturers can now monitor and track the production process in real-time. This allows for better quality control, reducing the risk of defects and recalls. Additionally, IoT enables automation of certain processes, making them more precise and less prone to human error.
How to Use IoT for Quality Control and Automation
To use IoT for quality control, companies can install sensors on machines and products and use cameras to monitor the production process. These sensors will collect data such as temperature, pressure, and movement, allowing companies to detect any anomalies or defects. Automation can also be achieved by integrating sensors, machines, and robots to perform specific tasks without human intervention.
Example: Heineken’s Smart Factory
Beer manufacturer Heineken has implemented IoT in their production process, creating a fully automated smart factory. The factory uses sensors and cameras to monitor the quality of the ingredients, production, and packaging. Any deviations from the standard are detected in real-time, allowing for immediate adjustments to maintain high-quality standards.
Comparison: Manual vs. Automated Quality Control
In manual quality control, human error can often result in defects and recalls, which can be costly for manufacturers. With IoT-enabled automated quality control, companies can reduce the risk of errors and ensure consistency in production. This ultimately leads to higher quality products and satisfied customers.
Advice: Implement IoT Gradually
When implementing IoT for quality control and automation, it is essential to do so gradually. Companies should start with small steps, such as installing sensors on a few machines or products, and then increase gradually. This approach allows for easier integration and helps identify any potential issues before they become major problems.
5. Enhanced Safety Measures
Safety is a top priority in the manufacturing industry, and IoT has significantly improved safety measures in factories. With the use of sensors, companies can monitor equipment and detect any potential hazards, such as overheating, leaks, or malfunctions. This real-time data can help prevent accidents and ensure the safety of employees, preventing costly lawsuits and damage to the company’s reputation.
How to Use IoT for Enhancing Safety
Companies can install sensors and cameras in their factories to monitor equipment, processes, and employees. The data collected can be analyzed to identify any potential hazards and take corrective action promptly. Additionally, wearable devices can also be used to track employee safety, such as detecting falls or accidents and sending alerts for immediate assistance.
Example: Airbus’ Wearable Technology
Airbus, an aircraft manufacturer, uses IoT-enabled wearable technology to improve safety for their employees. The device, known as “Smart Cap,” monitors the brainwaves of workers performing tasks that require high levels of concentration. If the device detects fatigue or stress levels that may compromise safety, an alert is sent to the worker and their supervisor.
Comparison: Traditional vs. IoT-Enabled Safety Measures
Traditional safety measures relied on manual inspections and reports, making them less efficient and prone to human error. With IoT-enabled safety measures, real-time data is collected and analyzed, allowing for better detection and prevention of hazards. This approach has proven to be more effective in ensuring workplace safety.
Advice: Train Employees on IoT Safety Protocols
To fully utilize the benefits of IoT for safety in manufacturing, it is essential to train employees on the protocols and procedures. They need to understand how IoT works, how to interpret the data, and what actions to take in case of an emergency. It is also crucial to have a system in place to handle any alerts or alarms that are triggered by the connected devices.
6. Cost Reduction and Increased Profitability
One of the main objectives of implementing IoT in manufacturing is to reduce costs and increase profitability. By automating processes, reducing downtime, and improving efficiency, companies can save both time and money. IoT also enables predictive maintenance, reducing maintenance costs and eliminating unexpected breakdowns. With improved product quality and safety, companies can also avoid costly recalls and lawsuits, ultimately increasing profitability.
How to Use IoT for Cost Reduction
To use IoT for cost reduction, companies can start by identifying areas in their manufacturing process where IoT can be applied. They can then invest in infrastructure, such as sensors and analytics tools, and train their workforce to utilize this technology effectively. Monitoring and analyzing data can help identify any areas for improvement and optimize processes for cost reduction.
Example: John Deere’s Smart Farming
John Deere, a leading agriculture machinery manufacturer, uses IoT to improve farming practices and reduce costs for farmers. The company uses sensors, cameras, and GPS technology to collect data from farm equipment and fields. They analyze this data to provide insights and recommendations to farmers on optimizing their operations, ultimately reducing costs and increasing profits.
Comparison: Costs Before and After IoT Implementation
Before the introduction of IoT, the manufacturing industry incurred significant costs due to manual labor, human error, and unexpected breakdowns. With the integration of IoT, companies have seen a reduction in these costs by automating processes, reducing downtime, and improving efficiency. This has resulted in increased profitability for many manufacturing companies.
Advice: Continuously Monitor and Improve
To fully utilize the cost-reducing benefits of IoT, it is crucial to continuously monitor and improve operations. Companies should use data collected from sensors to identify any areas for improvement and optimize processes. By doing so, manufacturers can stay competitive, reduce costs, and increase profitability.
FAQs
Q1. What is IoT in manufacturing?
A1. IoT (Internet of Things) in manufacturing refers to the use of interconnected devices and machines through the internet to collect and exchange data in real-time. This technology allows for better optimization, automation, and decision-making in the production process.
Q2. What are the benefits of using IoT in manufacturing?
A2. Using IoT in manufacturing has numerous benefits, such as improved efficiency, productivity, and safety. It also allows for predictive maintenance, enhanced quality control, and cost reduction, ultimately leading to increased profitability.
Q3. How can companies implement IoT in their manufacturing process?
A3. To implement IoT in manufacturing, companies need to invest in infrastructure, such as sensors, data storage, and analytics tools. They also need to train their workforce to understand and utilize this technology effectively. It is essential to identify areas in the manufacturing process that can benefit from IoT, such as supply chain management, inventory control, and quality control.
Q4. Is IoT expensive to implement in manufacturing?
A4. The cost of implementing IoT in manufacturing may vary depending on the size and complexity of the operations. However, with advancements in technology, the cost of IoT devices and infrastructure has decreased, making it more accessible for businesses of all sizes.
Q5. Is there a risk of security breaches with IoT in manufacturing?
A5. As with any technology, there is always a risk of security breaches with IoT. However, companies can mitigate this risk by investing in secure infrastructure, training employees on cybersecurity protocols, and continuously monitoring and updating their systems.
Conclusion
IoT has brought about a revolution in the manufacturing industry, transforming traditional factories into smart factories. With its ability to optimize processes, increase efficiency, improve quality control, and reduce costs, IoT has become an essential tool for manufacturers worldwide. To stay competitive in today’s market, companies must embrace digital transformation and adopt IoT in their operations. By doing so, they can reap the many benefits that this technology has to offer, ultimately leading to increased profitability and success in the global manufacturing industry.