With the increasing demand for efficient and smart production processes, the manufacturing industry is undergoing a significant transformation. One of the major driving forces behind this change is the adoption of Internet of Things (IoT) technology. The integration of IoT in manufacturing industry has revolutionized traditional manufacturing processes, making them more automated, data-driven, and connected. In this article, we will delve deeper into the world of IoT in manufacturing industry, exploring its benefits, applications, and future possibilities.
1. Understanding IoT in Manufacturing Industry
What is IoT?
Internet of Things, commonly known as IoT, is a network of interconnected devices that are equipped with sensors, software, and other technologies to collect and exchange data over the internet. This technology enables physical devices to communicate with each other, making it possible for machines, systems, and people to interact seamlessly without human intervention. In simple terms, IoT is a bridge between the physical and digital world, connecting everything from household appliances to industrial machinery.
What is IoT in Manufacturing Industry?
The application of IoT technology in the manufacturing industry is referred to as Industrial Internet of Things (IIoT) or simply IoT in manufacturing industry. It involves connecting various machines, sensors, and other devices used in the production process to a central network, enabling real-time data monitoring, analysis, and management. By leveraging the power of IoT, manufacturing companies can enhance their operational efficiency, reduce costs, and make smarter decisions based on insights derived from real-time data.
Advantages of IoT in Manufacturing Industry
The incorporation of IoT technology in manufacturing industry brings numerous benefits, some of which include:
- Enhanced Efficiency: IoT-enabled processes eliminate manual labor and streamline operations, resulting in improved productivity and reduced time and cost.
- Predictive Maintenance: With the help of IoT sensors and data analytics, manufacturers can monitor equipment performance in real-time and predict potential failures, allowing for timely maintenance and reduced downtime.
- Real-time Data Analysis: IoT enables data analysis in real-time, providing manufacturers with actionable insights to make informed decisions on production processes, quality control, and supply chain management.
- Improved Quality Control: By monitoring production processes in real-time, identifying defects and inefficiencies becomes easier, enabling manufacturers to improve product quality.
- Reduced Costs: With the automation of processes, manufacturers can reduce labor costs and minimize waste, leading to overall cost savings.
- Increased Safety: IoT sensors can monitor equipment performance and detect any malfunctions or safety hazards, ensuring a safe working environment for employees.
2. Applications of IoT in Manufacturing Industry
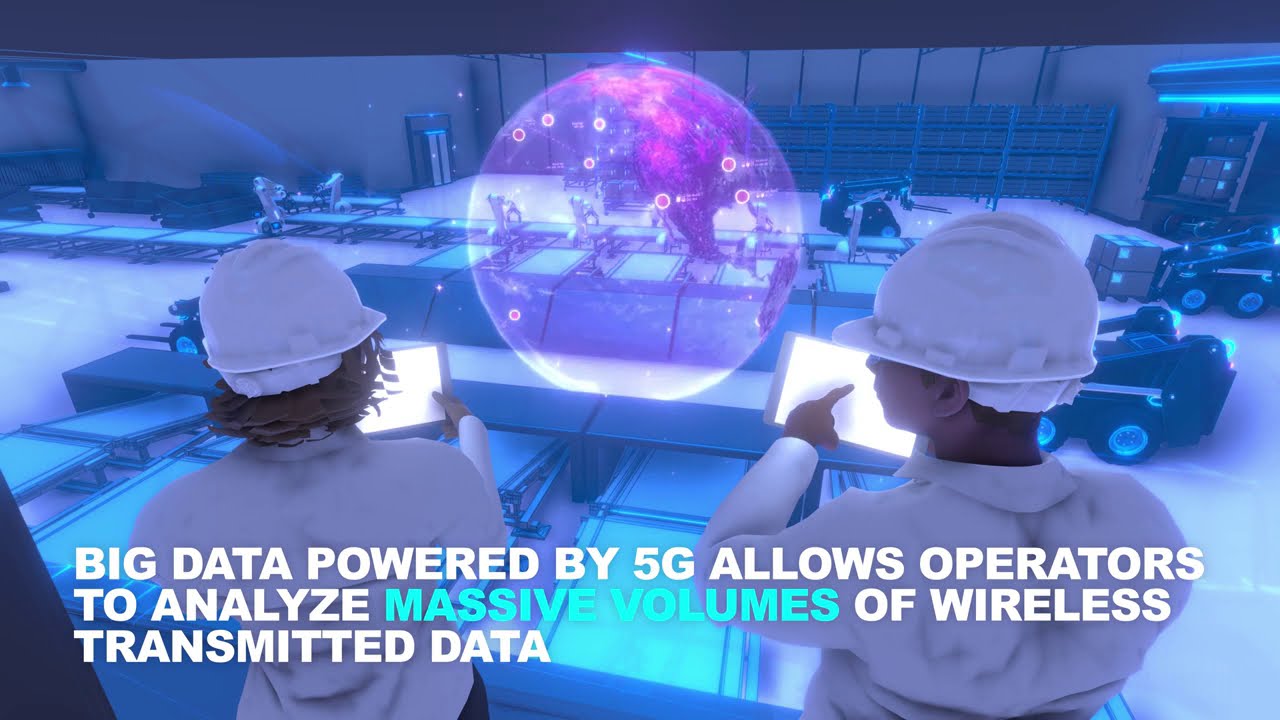
Supply Chain Management
One of the key areas where IoT has made a significant impact in the manufacturing industry is supply chain management. By integrating IoT sensors and devices into the supply chain, manufacturers can track inventory levels, monitor the condition of products during transit, and optimize distribution routes. This results in improved inventory management, reduced costs, and increased efficiency.
Predictive Maintenance
As mentioned earlier, IoT technology enables predictive maintenance, which involves continuously monitoring equipment performance and predicting when maintenance is required. This not only reduces the risk of unexpected breakdowns but also increases the lifespan of machinery, resulting in cost savings for manufacturers.
Quality Control
IoT-enabled devices, such as cameras and sensors, can be used to detect any defects or inconsistencies in the production process, ensuring that high-quality products are delivered to customers. By analyzing real-time data, manufacturers can identify patterns and trends in quality control, making adjustments and improvements where necessary.
Asset Management
The integration of IoT technology in manufacturing industry has also revolutionized asset management. By tracking and monitoring equipment in real-time, manufacturers can better manage their assets, optimize utilization rates, and reduce costs associated with over-maintenance or underutilization.
3. How to Use IoT in Manufacturing Industry
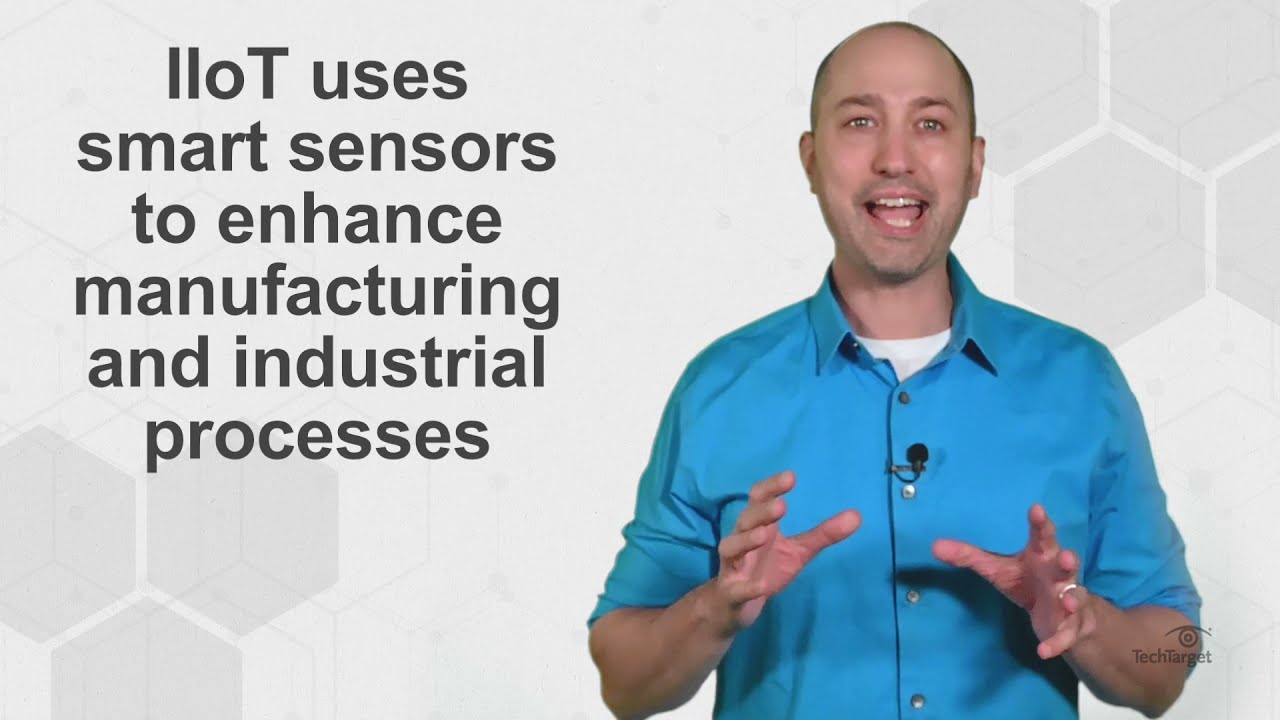
The implementation of IoT technology in manufacturing industry requires careful planning and execution. The following steps can guide companies in utilizing IoT for their production processes:
- Identify Key Areas: Begin by identifying key areas of your production process that can benefit from IoT technology, such as supply chain management, quality control, or asset management.
- Choose the Right Hardware and Software: Select IoT devices and sensors that are suitable for your production environment and can collect data accurately. Also, choose a reliable software platform that can handle large amounts of data and provide real-time analysis.
- Integrate with Existing Systems: To fully leverage IoT technology, it is crucial to integrate it with existing systems, such as Enterprise Resource Planning (ERP) or Customer Relationship Management (CRM) platforms.
- Train Employees: As with any new technology, it is essential to train employees on how to use IoT-enabled devices and the benefits of incorporating them into the production process.
- Monitor and Analyze Data: Regularly monitor and analyze data collected by IoT devices to identify patterns, trends, and areas for improvement.
4. Examples of IoT in Manufacturing Industry
General Electric (GE)
GE has been at the forefront of adopting IoT in its manufacturing processes. The company uses sensors and analytics to monitor the performance of its industrial machinery and predict potential issues, resulting in significant cost savings and increased efficiency.
BMW
BMW utilizes IoT technology in its production lines to track inventory levels, monitor equipment performance, and optimize assembly line processes. By doing so, the company has reduced costs, improved productivity, and enhanced product quality.
5. Comparing Traditional Manufacturing with IoT-enabled Manufacturing
Traditional manufacturing processes involve manual labor, long production cycles, and limited data collection and analysis. On the other hand, IoT-enabled manufacturing involves automated processes, real-time data analysis, and predictive maintenance. This results in improved efficiency, reduced costs, and better product quality.
6. Advice for Adopting IoT in Manufacturing Industry
- Start Small: Begin by incorporating IoT technology in a specific area of your production process to test its feasibility and benefits before scaling up.
- Ensure Data Security: With the collection of large amounts of data, it is crucial to have robust security measures in place to protect sensitive information from cyber threats.
- Choose the Right Technology Partner: Collaborate with an experienced and reliable technology partner who can guide you through the implementation process and provide ongoing support.
- Embrace Change: The adoption of IoT technology will bring about significant changes in your manufacturing processes. It is essential to be open to these changes and adapt to them to fully reap the benefits of IoT.
FAQs about IoT in Manufacturing Industry
Q1. What are some common challenges companies face when implementing IoT in manufacturing industry?
Answer: Some of the challenges include data security, integration with existing systems, and training employees on how to use IoT-enabled devices.
Q2. Can IoT technology be applied to all types of manufacturing processes?
Answer: Yes, IoT can be implemented in various manufacturing processes, including discrete, process, and mixed-mode manufacturing.
Q3. How does IoT technology improve supply chain management?
Answer: By monitoring inventory levels, tracking products during transit, and optimizing distribution routes, IoT technology can enhance supply chain management, leading to cost savings and increased efficiency.
Q4. Is IoT only beneficial for large manufacturing companies?
Answer: No, even small and medium-sized manufacturing companies can benefit from IoT technology, as it offers cost-effective solutions and helps improve efficiency.
Q5. What are some future possibilities of IoT in manufacturing industry?
Answer: With advancements in IoT technology, we can expect to see more automation, predictive analytics, and real-time monitoring in manufacturing processes.
Conclusion
The integration of IoT technology in manufacturing industry has opened up a world of possibilities, making production processes more efficient, connected, and data-driven. With real-time data analysis and predictive maintenance, manufacturers can make smarter decisions, reduce costs, and improve product quality. As IoT continues to evolve, we can only expect to see more innovative applications and advancements in the manufacturing industry. It is clear that IoT is here to stay and will continue to revolutionize the future of production.